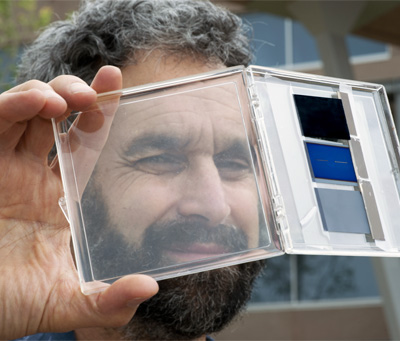
Howard Branz, principal scientist behind black silicon etching, holding silicon wafers (Credit: Dennis Schroeder -- NREL)
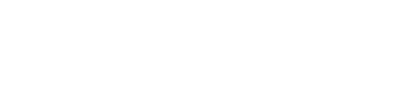
-
Optical Cavity Furnace
In October, the USDA’s National Renewable Energy Laboratory introduced a new way to manufacture solar cells that uses half the amount of energy as the traditional thermal process while costing significantly less. When crystalline silicon wafers are subjected to visible and near-infrared light within what developers have named the Optical Cavity Furnace, they heat up much as they would in a conventional thermal chamber but in less time and with greater uniformity, thus becoming more efficient. The NREL and its private industry partner AOS Inc. predict that by making use of these photonic effects, a planned industrial-scale Optical Cavity Furnace will be capable of producing 1,200 wafers per hour.
-
Silicon Ink
Another of NREL’s partnerships with a private business has paid off in the form of black goop. Who knew that clean renewable energy could be so mucky? Together with Innovalight, a California company recently acquired by DuPont, the laboratory has developed a liquid form of silicon that can be screen printed onto solar cells as an added varnish to increase efficiency by as much as 6 percent through better absorption of blue light. According to NREL, this so-called Silicon Ink has already been incorporated into the production lines of five of the world’s leading solar cell companies. It’s a low cost way to get more out of existing solar products. So in spite of its dark appearance, one might even call it liquid gold.